Distillation columns are the ubiquitous workhorses of the chemical processing industry. Design and optimization of these unit operations is done at a much higher level of fidelity than ever before using mass transfer models.
As students, we learned McCabe-Thiele diagrams and shortcut methods to solve simple distillation systems. Often, a little more complexity was added using a spreadsheet to solve harder problems. Then, of course, we were given access to a simulation program which used more rigorous methods, including simultaneous correction and/or inside-out algorithms. When it came to actual columns in the field, however, they didn't always achieve quite what the equilibrium-stage based calculations predicted. You could specify an overall efficiency or even stage-by-stage efficiency profiles to get a better match, but this was a crude way of dealing with the issue.
Enter mass-transfer models, like Bravo & Fair for random packing, Bravo, Rocha & Fair for structured packing, and Billet & Schultes for random or structured packing. CHEMCAD includes these models, along with a database of common packing coefficients. For trayed columns, we include the Chan-Fair, AIChE, and Zuiderweg tray models.
Defining the geometry of such a column requires more user input, but the payoff is vastly improved accuracy and realism in the results for product streams, energy usage, and pressure drop.*
So, take a moment to back up a copy of a simulation with distillation column(s); convert them to mass-transfer by specifying the actual trays/packing you're using; and enjoy the benefits of more accurate answers to your distillation calculations. If you have questions, or if you want to share your successes, give our technical staff a call today!
* I should mention here that from what I've seen in papers delivered by distillation experts over the years, column-internals installation issues can cause significant deviation from expected results in the field. There are a number of companies that specialize in identifying such issues, and I invite you to check out our friends, Dr. Frank Seibert & Dr. Bruce Eldridge, over at the University of Texas Separations Research Program if you're interested in applied research on this topic and more.
Wednesday, October 29, 2014
Wednesday, October 15, 2014
Did you know you can quickly make property calculations in CHEMCAD?
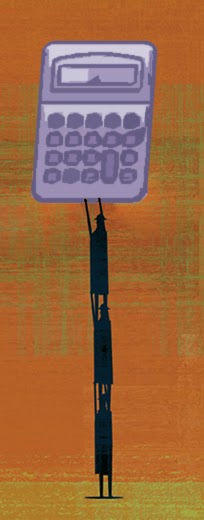
If you have an existing flowsheet with a stream already set up with the right composition, just double-click the stream, and you can immediately calculate bubble/dew point (T or P) or vapor fractions. Just remember Gibbs' phase rule and specify two of the three available fields (T, P, VF); then click the Flash button and you'll have your answer. To get at the thermophysical properties, just right-click the stream and select View Properties to get a quick report.
But what if you want to use a composition that isn't in your current flowsheet? If all the right chemicals are in your component list, and you've got the appropriate K-value and enthalpy methods selected, try this trick:
- Make sure no streams are selected (you can click in the white space of the flowsheet to be certain).
- On the CHEMCAD main menu, choose Specifications > Select Streams.
- In the input dialog, type a stream number not currently used in your flowsheet (like 999) and click OK.
Don't let your investment in simulation sit around waiting for the large projects! CHEMCAD is like having your own chemical engineering calculator, and it's ready to supercharge all of your tasks.
Whether you're working on a simulation of your entire process, sizing a few pieces of equipment, or just looking for a quick property calculation, don't hesitate to get in touch with our technical staff for more best-practices tips.
Thursday, October 9, 2014
Do we need more chemical engineers? Do we need more heroes?
Someone recently forwarded me a link to ExxonMobil's perspectives blog on the subject of engineers in the United States. You can take a look here to see Ken Cohen's take on addressing the need to educate and connect with young people about engineering and engineers--especially the societal impact, both past and present, of our profession.
As I pointed out several years ago, there are a couple of ways to attack this problem. ExxonMobil's site, BeAnEngineer, and their associated television commercials are a fantastic 'top-down' approach to get the message out to the general public. The complementary approach is 'bottom-up,' and their material is also a great resource for engineers who want to arm themselves with facts and figures they can use to have one-to-one or one-to-few conversations with young people or non-technical colleagues and acquaintances.
If we, as engineers, don't tell our story and tell it well, then we leave ourselves open to two serious consequences: (1) our story gets told by those who view chemicals and chemical engineering as inherently 'bad,' and (2) fewer young people are interested in pursuing chemical engineering.
You know the role we play in society now, and the role we'll play in the future. Learn more about our past successes. Tell your story. Tell our story. Be a hero.

If we, as engineers, don't tell our story and tell it well, then we leave ourselves open to two serious consequences: (1) our story gets told by those who view chemicals and chemical engineering as inherently 'bad,' and (2) fewer young people are interested in pursuing chemical engineering.
You know the role we play in society now, and the role we'll play in the future. Learn more about our past successes. Tell your story. Tell our story. Be a hero.
Friday, October 3, 2014
Congratulations to Trevor Rice, Outstanding Young Professional!
Our own Trevor Rice has been awarded the South Texas Section AIChE’s Outstanding Young
Professional Award for 2013!
Trevor is a valued member of the development team here at Chemstations, and we've seen his devotion to working on quality projects for our customers, so it's little surprise to us that his passion for the profession of chemical engineering has been rewarded by the local section leadership. He continues to contribute his time and effort to make STS a great institution, and we are all very proud of him and his efforts.
Trevor's award will be presented at the 6th AIChE Southwest Process Technology Conference at the Moody Gardens Conference Center and Hotel in Galveston, TX (October 9th and 10th, 2014; more information here). Chemstations technical and sales staff will be present throughout the conference, so stop by to congratulate Trevor and visit with us to chat about process simulation and CHEMCAD!
Trevor is a valued member of the development team here at Chemstations, and we've seen his devotion to working on quality projects for our customers, so it's little surprise to us that his passion for the profession of chemical engineering has been rewarded by the local section leadership. He continues to contribute his time and effort to make STS a great institution, and we are all very proud of him and his efforts.
Trevor's award will be presented at the 6th AIChE Southwest Process Technology Conference at the Moody Gardens Conference Center and Hotel in Galveston, TX (October 9th and 10th, 2014; more information here). Chemstations technical and sales staff will be present throughout the conference, so stop by to congratulate Trevor and visit with us to chat about process simulation and CHEMCAD!
Did you know CHEMCAD has flexible licensing options for individuals, groups, and companies?
Worrying about a license for your process simulator is probably not how you want to spend your time. We get it. You just want CHEMCAD to be available when you need it--so we try to make our licensing as invisible as possible to you, our customers and users.
To that end, we offer a variety of software and hardware licensing solutions, with the aim of providing a "set it and forget it" path for your organization:
Large organization (multi-user, multi-site, wide area network)
If you'd like to explore licensing options, you can browse the CHEMCAD knowledgebase on our customer portal, where you'll find articles that address common licensing questions. You can also get in touch with us directly, and let our staff show you how flexible and available CHEMCAD can be in your computing environment.

- System Authorization software keys for single-machine licensing
- SafeNet(TM) hardware keys for single-machine licensing
- SafeNet(TM) hardware keys for network licensing
- SafeNet(TM) RMS software keys for network licensing
Large organization (multi-user, multi-site, wide area network)
- Access a pool of licenses from any client computer on the network, served by a hardware key placed on any machine on the network.
- Access a pool of licenses from any client computer on the network, served by a software license server (RMS). This further allows commuting of licenses: for example, a laptop connected to your network can 'check out' a license and then leave your network to use CHEMCAD at a remote site.
- License a single, dedicated CHEMCAD machine with a software key.
- Share one or more hardware keys.
- Use either of the network options listed above on your local area network.
- License a single, dedicated CHEMCAD machine with a software key.
- Use a hardware key to enable the most convenient machine (desktop, laptop, etc.) at any given time.
If you'd like to explore licensing options, you can browse the CHEMCAD knowledgebase on our customer portal, where you'll find articles that address common licensing questions. You can also get in touch with us directly, and let our staff show you how flexible and available CHEMCAD can be in your computing environment.
Wednesday, September 24, 2014
Did you know you can model aqueous electrolyte systems in CHEMCAD?
Water. It's in almost every plant and system . . . if it's not in your process streams, it's likely in your utilities. If your process is defined by aqueous electrolytes, you've probably already been modeling or planning to model concentration, boiling point rises, precipitation, pH, and so forth.
CHEMCAD has both the modified NRTL and Pitzer thermodynamic systems built right in. They are available for calculation in any unit operation, including distillation columns. With mNRTL, you can run in apparent species or true species modes (we have a great discussion on the pros & cons of each in our help system, and we'd be happy to go over it with you). There are a significant number of common electrolyte species and electrolyte reaction data sets included with the program. If you don't have reaction equilibrium constants, CHEMCAD will estimate them from Gibbs free energy of formation for the electrolyte species or you can regress from laboratory/experimental data.
Even if you don't have electrolytes in your process streams, you can still benefit from this feature: if you'll recall from a prior post on modeling utilities (here), there are economic benefits to analyzing your cooling water system. You can watch the buildup of carbonates or other salts, to determine optimal bleed/purge rates or timing for injection of cleaning chemicals.
To jump-start your next aqueous electrolyte modeling work, get in touch with us--we'd love the chance to help make your project a positive one!
CHEMCAD has both the modified NRTL and Pitzer thermodynamic systems built right in. They are available for calculation in any unit operation, including distillation columns. With mNRTL, you can run in apparent species or true species modes (we have a great discussion on the pros & cons of each in our help system, and we'd be happy to go over it with you). There are a significant number of common electrolyte species and electrolyte reaction data sets included with the program. If you don't have reaction equilibrium constants, CHEMCAD will estimate them from Gibbs free energy of formation for the electrolyte species or you can regress from laboratory/experimental data.
Even if you don't have electrolytes in your process streams, you can still benefit from this feature: if you'll recall from a prior post on modeling utilities (here), there are economic benefits to analyzing your cooling water system. You can watch the buildup of carbonates or other salts, to determine optimal bleed/purge rates or timing for injection of cleaning chemicals.
To jump-start your next aqueous electrolyte modeling work, get in touch with us--we'd love the chance to help make your project a positive one!
Tuesday, September 16, 2014
Did you know you can model a vessel reactor in CHEMCAD?
Do you have an existing vessel reactor in your process? Often, we hear from customers that they have an existing operating procedure, but they aren't sure exactly how much time the reaction actually requires.
Maybe you have a basic reaction analysis from an R&D group that requires scale-up from the lab to a full-scale vessel reactor. We've worked with organizations that would like to use the same software tool for R&D, process development, and operations.
CHEMCAD has you covered.
It's helpful to think of reaction systems in four parts: (1) the reactants/products/by-products, (2) the reaction, (3) the vessel, and (4) the operation step(s).
For the chemicals, CHEMCAD's database of physical properties includes all the DIPPR(TM) data for pure compounds, as well as a wide variety of methods for calculating mixture properties and the phase equilibria.
For the reaction, you can specify Arrhenius constants (or extended Langmuir-Hinshelwood constants), or you can define your own reaction equation for ultimate flexibility. If you don't yet have the kinetics worked out, CHEMCAD also includes regression facilities that you can use with laboratory or operating data.
For the vessel, you can simulate everything from a laboratory flask to a full-scale, continuously stirred tank reactor (CSTR) with jackets and coils. You can define ancillary equipment like pumps, control valves, and PID controllers for feed streams, product streams, and utilities. Add a vent condenser or even a distillation column to the top of the reactor. You can even model safety scenarios by adding relief devices to the vessel.
For the operation step(s), CHEMCAD's dynamic simulation system allows you to set run times, control schemes, dosing rates, ramp controls, and more. CHEMCAD will rigorously calculate properties, reaction rates, phase equilibria, pressure (if desired), and heat transfer for heating/cooling systems. You'll see volume, composition, temperature, pressure, and more versus time so you can optimize your design or your existing operations. And, of course, you can model batch, semi-batch, or continuous operation.
Want to join the ranks of customers who've successfully designed and optimized their vessel reactors? Contact your CHEMCAD sales or support representative today!
Maybe you have a basic reaction analysis from an R&D group that requires scale-up from the lab to a full-scale vessel reactor. We've worked with organizations that would like to use the same software tool for R&D, process development, and operations.
CHEMCAD has you covered.
It's helpful to think of reaction systems in four parts: (1) the reactants/products/by-products, (2) the reaction, (3) the vessel, and (4) the operation step(s).

For the reaction, you can specify Arrhenius constants (or extended Langmuir-Hinshelwood constants), or you can define your own reaction equation for ultimate flexibility. If you don't yet have the kinetics worked out, CHEMCAD also includes regression facilities that you can use with laboratory or operating data.
For the vessel, you can simulate everything from a laboratory flask to a full-scale, continuously stirred tank reactor (CSTR) with jackets and coils. You can define ancillary equipment like pumps, control valves, and PID controllers for feed streams, product streams, and utilities. Add a vent condenser or even a distillation column to the top of the reactor. You can even model safety scenarios by adding relief devices to the vessel.
For the operation step(s), CHEMCAD's dynamic simulation system allows you to set run times, control schemes, dosing rates, ramp controls, and more. CHEMCAD will rigorously calculate properties, reaction rates, phase equilibria, pressure (if desired), and heat transfer for heating/cooling systems. You'll see volume, composition, temperature, pressure, and more versus time so you can optimize your design or your existing operations. And, of course, you can model batch, semi-batch, or continuous operation.
Want to join the ranks of customers who've successfully designed and optimized their vessel reactors? Contact your CHEMCAD sales or support representative today!
Wednesday, September 10, 2014
Did you know you can perform an optimization in CHEMCAD?
Your process (or process design) is probably not fully optimized. Of course, you know that, and you own a simulator to improve your process. For example, you may make a relatively simple calculation like finding the optimal feed tray location in a distillation column.
In our training courses, we teach a simple method of using CHEMCAD's sensitivity analysis to vary feed tray location while measuring reboiler duty, and we've heard back from a number of you who've achieved significant savings from doing just that.
But did you know that you can have CHEMCAD do the work for you? This is not only possible, but also very straightforward.
Included with CHEMCAD is an optimizer (using General Reduced Gradient, Successive Quadratic Programming, or Simultaneous Modular SQP routines) that allows you to define an objective function and tell the program which variables it can adjust in order to find the optimum (min/max). After just a few clicks, you'll have your solution.
Now let's go even further: many dedicated optimization engines allow "multi-variable" optimization, but you don't need to look beyond the software you already have.
An easy-to-understand example is a CAPEX/OPEX calculation, designed to find the optimal allocation of resources over a given period of time. Using CHEMCAD's cost algorithms, you can get a total equipment cost and an operating cost (energy, utilities, feeds, etc.), which can all be fed to an Excel(TM) spreadsheet using CHEMCAD's Data Map. Another approach to calculating the CAPEX and OPEX values and ratio would be to write a routine in CHEMCAD's Visual Basic for Applications (VBA) tool. The ratio is then available as your objective function in the optimizer.
We told you money was hiding in your process--isn't it time you went out and got it?
To find out more, get in touch with our sales or support representatives. Happy optimizing!
In our training courses, we teach a simple method of using CHEMCAD's sensitivity analysis to vary feed tray location while measuring reboiler duty, and we've heard back from a number of you who've achieved significant savings from doing just that.
But did you know that you can have CHEMCAD do the work for you? This is not only possible, but also very straightforward.
Included with CHEMCAD is an optimizer (using General Reduced Gradient, Successive Quadratic Programming, or Simultaneous Modular SQP routines) that allows you to define an objective function and tell the program which variables it can adjust in order to find the optimum (min/max). After just a few clicks, you'll have your solution.
Now let's go even further: many dedicated optimization engines allow "multi-variable" optimization, but you don't need to look beyond the software you already have.
An easy-to-understand example is a CAPEX/OPEX calculation, designed to find the optimal allocation of resources over a given period of time. Using CHEMCAD's cost algorithms, you can get a total equipment cost and an operating cost (energy, utilities, feeds, etc.), which can all be fed to an Excel(TM) spreadsheet using CHEMCAD's Data Map. Another approach to calculating the CAPEX and OPEX values and ratio would be to write a routine in CHEMCAD's Visual Basic for Applications (VBA) tool. The ratio is then available as your objective function in the optimizer.
We told you money was hiding in your process--isn't it time you went out and got it?
To find out more, get in touch with our sales or support representatives. Happy optimizing!
Tuesday, September 2, 2014
Did you know that CHEMCAD has offered embedded rigorous heat exchanger modeling for over eight years?
CHEMCAD's CC-THERM module has offered embedded rigorous modeling of heat exchangers for many years. Why is this a valuable tool?
In many cases, general heat transfer calculations for exchangers are sufficient. In other circumstances, though, you really need a more rigorous model. Let's look at a few examples where rigorous heat exchanger modeling can help you obtain faster, more accurate results.
Imagine you're a plant engineer and are asked to find a way to improve throughput. Can your existing heat exchangers handle the increased flow? You can use CC-THERM in Rating mode to enter specifications for the existing exchanger (TEMA type, # of tubes, baffles, etc.) and get the flows, temperatures, and pressures to match current conditions. Then increase the flow in the model to see if you exceed any constraints on the exchanger.
Suppose there's a concern with fouling in a particular stream. You can switch to Fouling Rating mode in CC-THERM to calculate the fouling rate that allows the model to fit reality. Then increase the flow in the model as before, to determine whether the existing exchanger will be sufficient.
Is the exchanger you have not big enough to handle the increased throughput? You can use CC-THERM in Design mode to design a replacement exchanger. Use the specifications of the existing exchanger to create your initial estimates, since you know these specs are close to your requirements. Now you can approach your heat exchanger manufacturers with a much clearer picture of what you need and what their proposed design should look like.
CC-THERM is available as a stand-alone product or as an add-on to your existing CHEMCAD package. Please contact us at 1-800-CHEMCAD for more details!
In many cases, general heat transfer calculations for exchangers are sufficient. In other circumstances, though, you really need a more rigorous model. Let's look at a few examples where rigorous heat exchanger modeling can help you obtain faster, more accurate results.
Imagine you're a plant engineer and are asked to find a way to improve throughput. Can your existing heat exchangers handle the increased flow? You can use CC-THERM in Rating mode to enter specifications for the existing exchanger (TEMA type, # of tubes, baffles, etc.) and get the flows, temperatures, and pressures to match current conditions. Then increase the flow in the model to see if you exceed any constraints on the exchanger.
Suppose there's a concern with fouling in a particular stream. You can switch to Fouling Rating mode in CC-THERM to calculate the fouling rate that allows the model to fit reality. Then increase the flow in the model as before, to determine whether the existing exchanger will be sufficient.
Is the exchanger you have not big enough to handle the increased throughput? You can use CC-THERM in Design mode to design a replacement exchanger. Use the specifications of the existing exchanger to create your initial estimates, since you know these specs are close to your requirements. Now you can approach your heat exchanger manufacturers with a much clearer picture of what you need and what their proposed design should look like.
CC-THERM is available as a stand-alone product or as an add-on to your existing CHEMCAD package. Please contact us at 1-800-CHEMCAD for more details!
Friday, August 15, 2014
Did you know that CHEMCAD is great for modeling utilities?
Steam. Cooling water. Thermal fluids. Air. Nitrogen. Fuel. Almost every facility
has them, and they can represent a great opportunity to improve your processes’
efficiency and reduce costs. Knowing if your equipment (pumps, compressors, cooling towers, heat exchangers, piping, etc.) is properly sized and
your maintenance regimen (water treatment, equipment cleaning, etc.) is properly timed can represent both capital and operating
cost improvements. This topic is covered in some detail in our training
courses, and I’ve seen the “idea bulb” above trainees' heads when they realize
the ease with which they can chase down significant process improvements.
One example we cover is the use of a distillation column
UnitOp to model a cooling tower. You can add as much or as little complexity to
the simulation as you like, and in our training course, we even go into details
such as aqueous electrolytes and blowdown. We’ve also helped customers with
models of incredibly extensive piping networks that deliver steam and cooling
water throughout large facilities. Again, depending on your needs, the level of detail can vary, but we’ve seen
everything from simple heat and material balances all the way to rigorous
piping pressure-drop calculations, control valves, dynamic response, and even
reverse flow (more on reverse flow and hydraulic balancing in a future post
here--stay tuned).
Just remember: don’t let the process side dominate your
thinking about how and when to use process simulation software. The utility side
can be just as important and valuable!
If you need some help getting started, contact our technical
support group, and we can direct you to an example or discuss your specific
questions.Did you know that you don’t have to commit to a long-term contract for CHEMCAD?
Think process simulation is only available on long-term
contracts? Well, depending on your particular situation, you may only need
CHEMCAD for a short duration, so a multi-year contract may not be right for
you. That’s why we offer a wide variety
of contract terms to fit your needs and your budget.
CHEMCAD is certainly available with one-, three- and five-year
contracts if you have longer-term needs, and there are discounts available as
the contract term increases. There are
even discounts for prepaying the entire contract term up front. However, if your needs are shorter-term, we
offer monthly contracts that allow you to align your simulation needs with your
projects. And if you decide to convert to a longer-term contract, we’ll credit
some of what you’ve paid on past monthly contracts.
What if you have a longer-term project but with limited needs for
simulation during the workflow? We’ve got you covered with our hourly usage
contracts. We’ll load your licensing
device with a pool of hours that can be used over the term of the contract, to lower
the cost of simulation versus our unlimited-use contracts.
And remember, if you need multiple simultaneous users, you
can take advantage of reduced prices for multiple licenses on any of our
contract types.
Don't hesitate to get in touch with one of our sales
staff or distributors around the world to discuss your situation. Whatever your simulation needs, we’ve got a
solution to fit!
Did you know that CHEMCAD is an OPC Server?
As you probably know, OPC (see more at the OPC Foundation, here)
is a standard for exchanging data in industrial automation. Commonly used in
the process industries by DCS, SCADA, and data historian systems, it also has
some very interesting benefits when combined with a process simulator.

You'll need to spend a little more effort to ensure that you have a validated model of your process (the simulation matches your plant performance within a tolerance you're comfortable with, and it reacts to process changes correctly). Many of you already go to this level of detail with your "offline" use of simulation software.
Imagine having alarms built into your SCADA system that can alert operations staff to deviations in plant performance versus design specifications! There are even installations of advanced process control (APC) using rigorous CHEMCAD simulations to improve process efficiency by linking SCADA systems, simulations, and economic optimization engines.
We’ve helped many customers do all of the above and more, so
give our support team a call if you’re thinking about a project and want to
understand CHEMCAD’s OPC Server capabilities.
Thursday, August 14, 2014
A New Blog Series: Did you know . . . ?
We’re starting a new series of topics here on the blog,
which will highlight some of the more useful applications and features of
CHEMCAD. Some of these will be high-level, powerful ways to use the program,
and some of them will be day-to-day, quick methods to get useful information
and analysis. Beyond that, we’ll cover some of the things you may not know
about CHEMCAD licensing and support. We’re rolling out our first few topics today, and will be adding content on a semi-regular basis.
Be sure to watch for these blog entries! In the meantime,
you can read on to discover why we’re doing this.
When I first got into the process simulation business 20
years ago, software was used in a slightly different way than it is today,
mostly owing to the speed of computing and available software development tools
back then. Large simulations took a long time to run—often they were left to
run overnight. (Those of you who remember coming into the office in the morning
only to find that your simulation failed to converge sometime after midnight, I
sympathize!) Also, because of the perceived complexity of the software, simulations
were often run only by in-house experts.
When graphical user interfaces came along, users could
finally do simple calculations easily, to get quantitative and qualitative
process data and display it in graphical form. I remember, for example, when CHEMCAD
users found they could quickly calculate bubble and dew points using the
simulator to get insight into their processes without having to build an entire flowsheet.
Nowadays, of course, this type of work is taken for granted.
Many of you regularly connect simulations to spreadsheets, math solvers, plant
data historians, SCADA systems, and more. Computing power has advanced to the
point where incredibly complex simulations can be run multiple times per day
(or even left to run at multiples of real-time for operator training and
advanced process control). And today, simulations are run by people with a wide
array of job functions within an engineering group.
Let me get back to the point: process simulation has
developed a wealth of features beyond simple heat and material balance
calculation, yet we find most users only use about 20% of the power available
to them. Some of this is due to the complexity of features; if you think of the
additional equipment geometry data required to run a rigorous dynamic
simulation, it’s often regarded as “too much effort,” despite the potential benefit! Other times, users simply don’t
realize that a feature is available. CHEMCAD has a wealth of features and power
just hidden from view—in some cases on purpose, as we strive to keep complexity
from hindering your day-to-day workflow.
Our staff can easily communicate about these features when
we have one-on-one conversations with customers. Our sales, technical support,
and training staff are always on hand to explain and walk through applications
of the program, but it isn’t every day that we get a chance to speak with you.
If we tried to make a brochure or set of documents to cover everything we want
to showcase, we’d end up with hundreds of pages for you to navigate.
What we hope to accomplish, then, is to spark some ideas
here with short descriptions in blog format. They’ll be quick reads which you
can compare to what you’re trying to accomplish in your role as a chemical
engineer. We hope that some of them will be immediately useful, and maybe
you’ll store one of them away in your brain and use it later for that “aha!”
moment.
We encourage you to jump in with your comments—let us know
which of these topics are new to you, how you might see them helping in your
simulation tasks, or what else you’d like to see covered in future blog
entries.
Subscribe to:
Posts (Atom)