Our own Fred Justice attended the recent (ASEE) American Society for Engineering Education 2010 Annual Conference and Exposition to help present the 2010 Chemstations Lectureship Award. Fred had a chance to catch up with longtime friends and to make some new ones in Louisville. The winner this year was Dr. Frank Doyle from the University of California, Santa Barbara for his work, "Research at the Interface of Control and Biology."
Last year's winner was Dr. Antonios Mikos from Rice University for his efforts, "Building a Better Biomaterial." The 2008 Winner was Dr. Jennifer Sinclair Curtis from University of Florida for her work, "Simulation of Particulate Flow Processes." Our belated congratulations to them both, also!
We've been fortunate and proud to be a part of the good work done by the ASEE, especially in advancing research and teaching in the field of chemical engineering. We wish our winners well and look forward to hearing more good things from them in the future.
Wednesday, July 7, 2010
Tuesday, March 16, 2010
Chemical Engineers are Heroes
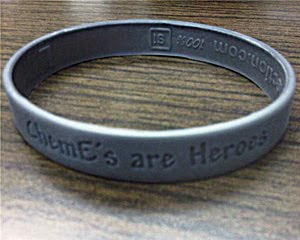
So if top-down campaigns are having limited impact, what about a bottom-up, grassroots message? A simple one like “Chemical Engineers are Heroes.”
We have probably all had the experience of having to quickly educate someone as to the number of products in their daily lives that would not (indeed, could not) exist without chemistry and the refining/chemical industry. Shoes, clothing, personal care products, makeup, perfumes, automobiles, paper products . . . the list is endless. Take a step further and think about all the advances in materials chemistry that make computing/electronics what they are today. And yet, “chemical engineer” represents something nefarious to many.
But it is chemical engineers who will be called upon to design and build new energy sources, new battery technologies, and processes to better clean effluent streams from chemical and power plants. We will be a part of plans to help bring food and fresh water to the planet’s growing population. We will continue to help improve the standard of living across the globe. We will increase the efficiency of today’s chemical processes, and we will help develop tomorrow’s processes.
So I considered a campaign to tell the world that you, as chemical engineers, are heroes. Something simple that wouldn’t be about anything other than bringing some positive attention to our education and careers. It isn’t always why we chose chemical engineering to start with, but it is why many of us are dedicated to the profession. It is why, up and down the halls of Chemstations, we’re all members of the American Institute of Chemical Engineers. It is why we support the activities of the AIChE. We’re proud of chemical engineering and we’re proud of you, the world’s chemical engineers.
Come see us at an upcoming industry meeting or trade show (our web site lists these events). Of course our sales staff will be happy to talk to you about the latest features in CHEMCAD, but come by and spend some time with our customer support engineers and our development staff . . . and we’ll have a free “ChemE’s are Heroes” wristband waiting for you.
CHEMCAD around the worldand some useful shortcuts
This blog entry is being written on a plane, somewhere between Mumbai/Bombay and Newark. Did you know that CHEMCAD is a global program? At last count, the software is being used in more than 70 countries around the world. I frequently visit our distributors, to help ensure that they can give the same level of support to their customers that we demand from our own employees.
While presenting some case studies of CHEMCAD use, I recently showed a roomful of engineers a hidden feature of CHEMCAD which is very useful. We sometimes hear, “Learning this feature alone was almost worth the cost of training!” So, I decided to share this trick—and a few others that I like—with our blog readers.
Engineering units are a constant frustration when you work across international borders. The default engineering units of CHEMCAD are English units, because the program was written by engineers in the USA. You probably know that the Format > Engineering Units command enables you to select different units (you can even specify local gauge pressure and reference temperature for standard vapor volume flow rate). But did you know that CHEMCAD has a handy units converter?
To use this fe
ature, open any Edit Streams dialog and click the mouse in the temperature field. Now press the [F6] key on your keyboard. The Temperature units converter will appear, as shown at left. Type a number and then press [ENTER] to convert it. Better yet, click OK to send the converted value back to the flowsheet!
Any dialog box field th
at has an engineering units label should display the correct units conversion tool when you press [F6]. When you use [F6] with the cursor in a field without units, or when you don’t have a dialog open at all, CHEMCAD displays the Engineering Units Converter, shown below. Here, you can choose the type of units to convert. (Users who have been with us since the DOS version of CHEMCAD may remember that there was once a European-to-US clothing size converter, as an Easter egg.)
Since I’m talking about one overlooked but useful feature, I might as well mention a few others that I rely upon:
While presenting some case studies of CHEMCAD use, I recently showed a roomful of engineers a hidden feature of CHEMCAD which is very useful. We sometimes hear, “Learning this feature alone was almost worth the cost of training!” So, I decided to share this trick—and a few others that I like—with our blog readers.
Engineering units are a constant frustration when you work across international borders. The default engineering units of CHEMCAD are English units, because the program was written by engineers in the USA. You probably know that the Format > Engineering Units command enables you to select different units (you can even specify local gauge pressure and reference temperature for standard vapor volume flow rate). But did you know that CHEMCAD has a handy units converter?
To use this fe

Any dialog box field th

Since I’m talking about one overlooked but useful feature, I might as well mention a few others that I rely upon:
- Look at the Palette pane on the right side of the CHEMCAD screen. See the capital T symbol near the top? You can use this tool to add a text box to the flowsheet. I like to use this for simulation notes, but you can also dress up your text with the other drawing tools seen here—rectangles, lines, polygons—or even an imported graphics file.
- For text that will not be displayed on the flowsheet, just click the Notes tab at the bottom of the workspace and start typing. This is another convenient way to keep notes with the simulation.
- If you make a plot from the Plot menu, you can then use the Chart menu to export the plot’s data points to a table in MS Excel.
- Using a wheel mouse? Hold the wheel button down to click and drag the view of your flowsheet. You can also scroll the center wheel forward or back to zoom in or out, respectively.
- Find the section of the CHEMCAD toolbar that contains the various ‘zoom’ items. One of them is Zoom to fit. This resizes your view of the flowsheet to fit everything in the window.
Monday, February 22, 2010
Informex 2010 and Green Engineering
The show
I visited the most recent Informex show put on by UBM and SOCMA in San Francisco last week. I was very interested in seeing the messaging that manufacturers were using to communicate their products and services to each other. Has the messaging changed since the global downturn?
It appears that for the majority of the exhibitors, the booths and brochures are still focused on the basics: Here is our product list, inquire for prices and delivery. However, I saw a significant number of exhibitors that were aggressively touting their companies' value-add: quality, post-deal service, speed, and custom products/services. It was good to see these companies really setting themselves apart in what's obviously a very competitive landscape. I'll be visiting with our staff here to see how best to position Chemstations to be a part of our customers' plans to remain competitive and successful.
Seeing green
I attended the "Green Chemistry Breakfast Briefing" on Friday morning and listened to three presentations by representatives from industrial companies regarding their implementations of Green Chemistry and Green Engineering. The meeting was produced by the ACS Green Chemistry Institute. I learned a little about the initiatives in place to create an ANSI standard, a "Greener Chemicals Product and Process Standard." I'm interested to hear whether this will end up as a self-certifying procedure or whether it will follow the ISO standard certification path and require third-party labs to be involved. I'm sure all the stakeholders have strong opinions!
All the presenters emphasized that there have been strong economic drivers to using these Green methodologies: lower energy usage, less waste, less recycle of solvents, and so forth. Following the presentations, I was left with a question that always comes up when discussing this type of optimization (Green or not): How do you manage the tradeoffs between optimization/efficiency/Green and operating flexibility?
In today's dynamic, global market, a manufacturer needs single-product flexibility (make more or less to suit market demand), as well as multi-product flexibility (make a product slate using existing facilities to suit market demand). If you optimize a single product or process, you may lose both types of flexibility. The panel tolerated my question with varying degrees of enthusiasm, but the message I came away with is that in the short term, the tradeoffs are more severe, but with long-term planning of products, processes, equipment, and facilities, there will be fewer tradeoffs.
Finally, I'd like to post the "12 Principles of Green Engineering" as described by Anastas & Zimmerman ("Design through the Twelve Principles of Green Engineering", Env. Sci. and Tech., 37, 5, 95, 101, 2003.):
Talk back
I'd really like your feedback and thoughts on these topics. I can envision a spreadsheet-scorecard for a process flowsheet generated in CHEMCAD to give qualitative comparisons of processes, and maybe even some quantitative analysis for the future ANSI standard. Who knows, maybe some of you are already doing just that. Let us know!
I visited the most recent Informex show put on by UBM and SOCMA in San Francisco last week. I was very interested in seeing the messaging that manufacturers were using to communicate their products and services to each other. Has the messaging changed since the global downturn?
It appears that for the majority of the exhibitors, the booths and brochures are still focused on the basics: Here is our product list, inquire for prices and delivery. However, I saw a significant number of exhibitors that were aggressively touting their companies' value-add: quality, post-deal service, speed, and custom products/services. It was good to see these companies really setting themselves apart in what's obviously a very competitive landscape. I'll be visiting with our staff here to see how best to position Chemstations to be a part of our customers' plans to remain competitive and successful.
Seeing green
I attended the "Green Chemistry Breakfast Briefing" on Friday morning and listened to three presentations by representatives from industrial companies regarding their implementations of Green Chemistry and Green Engineering. The meeting was produced by the ACS Green Chemistry Institute. I learned a little about the initiatives in place to create an ANSI standard, a "Greener Chemicals Product and Process Standard." I'm interested to hear whether this will end up as a self-certifying procedure or whether it will follow the ISO standard certification path and require third-party labs to be involved. I'm sure all the stakeholders have strong opinions!
All the presenters emphasized that there have been strong economic drivers to using these Green methodologies: lower energy usage, less waste, less recycle of solvents, and so forth. Following the presentations, I was left with a question that always comes up when discussing this type of optimization (Green or not): How do you manage the tradeoffs between optimization/efficiency/Green and operating flexibility?
In today's dynamic, global market, a manufacturer needs single-product flexibility (make more or less to suit market demand), as well as multi-product flexibility (make a product slate using existing facilities to suit market demand). If you optimize a single product or process, you may lose both types of flexibility. The panel tolerated my question with varying degrees of enthusiasm, but the message I came away with is that in the short term, the tradeoffs are more severe, but with long-term planning of products, processes, equipment, and facilities, there will be fewer tradeoffs.
Finally, I'd like to post the "12 Principles of Green Engineering" as described by Anastas & Zimmerman ("Design through the Twelve Principles of Green Engineering", Env. Sci. and Tech., 37, 5, 95, 101, 2003.):
The Twelve Principles of Green Engineering
- Inherent Rather Than Circumstantial
Designers need to strive to ensure that all materials and energy inputs and outputs are as inherently nonhazardous as possible. - Prevention Instead of Treatment
It is better to prevent waste than to treat or clean up waste after it is formed. - Design for Separation
Separation and purification operations should be designed to minimize energy consumption and materials use. - Maximize Efficiency
Products, processes, and systems should be designed to maximize mass, energy, space, and time efficiency. - Output-Pulled Versus Input-Pushed
Products, processes, and systems should be "output pulled" rather than "input pushed" through the use of energy and materials. - Conserve Complexity
Embedded entropy and complexity must be viewed as an investment when making design choices on recycle, reuse, or beneficial disposition. - Durability Rather Than Immortality
Targeted durability, not immortality, should be a design goal. - Meet Need, Minimize Excess
Design for unnecessary capacity or capability (e.g., "one size fits all") solutions should be considered a design flaw. - Minimize Material Diversity
Material diversity in multicomponent products should be minimized to promote disassembly and value retention. - Integrate Material and Energy Flows
Design of products, processes, and systems must include integration and interconnectivity with available energy and materials flows. - Design for Commercial "Afterlife"
Products, processes, and systems should be designed for performance in a commercial "afterlife." - Renewable Rather Than Depleting
Material and energy inputs should be renewable rather than depleting.
Talk back
I'd really like your feedback and thoughts on these topics. I can envision a spreadsheet-scorecard for a process flowsheet generated in CHEMCAD to give qualitative comparisons of processes, and maybe even some quantitative analysis for the future ANSI standard. Who knows, maybe some of you are already doing just that. Let us know!
Subscribe to:
Posts (Atom)